What is 5S?
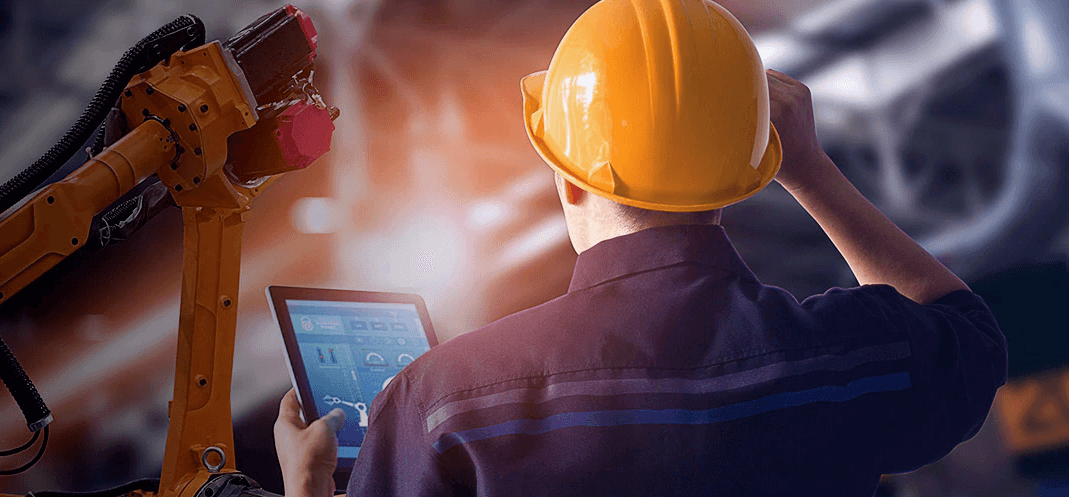
5S is a guideline structure for organizing the workplace so that work can be performed safely and effectively. It focuses on putting everything in the right places and maintaining a neat and tidy workplace that makes it easier for staff and workers to do their jobs without risking injury or wasting time. This lean manufacturing
5S Explained
Each “S” represents a part of the 5-step process which can improve the overall functioning of a business.
1. Sort
Sort is the first step. This involves going through all the materials, tools, equipment, furniture, and other items in a work area. Then, it helps determine what can be removed and what needs to be present.
To determine which is which, you need to consider several things in mind:
- What’s the purpose of the item?
- Does it really need to be here?
- How frequently is it used?
- When was the last time it was used?
- Who uses it?
2. Set
Now that the extra clutter is gone, work groups can now sort through the remaining items. In this step, you need to ensure that all remaining items are set in order, organized, and have a designated place.
By organizing all items left in the workplace in a logical way, workers can easily and efficiently complete their tasks.
3. Shine
This stage of 5S concentrates on cleaning up the work area. This literally means dusting, sweeping, moping, putting materials and tools away, wiping down surfaces, and others to make the work area nice and shiny.
In addition to the basic cleaning, this stage also includes regular maintenance of machinery and equipment.
4. Standardize
Things should look pretty good by now. All the unnecessary stuff is gone, everything’s organized, the workspace is shining brightly and all your equipment should be in good working condition.
Unfortunately, everything slowly slides back to the way they were. This 4th step makes the 5S system different from the usual spring-cleaning projects of businesses. Standardize is what systematizes the previous steps and turns the one-time effort into traditions or habits.
In this step, you will need to create schedules, assign regular tasks, and posting instructions in order for these cleaning and organizing activities to become routines. This ensures that orderliness does not fall by the wayside.
5. Sustain
Once the standard procedures for 5S are established, businesses need to perform the ongoing work of maintaining such procedures and improving or reforming them as necessary.
This last step ensures that the 5S runs smoothly, but also keeps everyone involved. Sustain aims to make 5S become a long-term program and become a part of the organization’s culture.
Safety: The Sixth S
Businesses also like to include a sixth S, which stands for Safety, in their 5S program. This step involves eliminating risks of injuries and damages in work processes by arranging things in specific ways.
This can involve setting up ergonomic stations, labeling storage cabinets for hazardous chemicals, putting up signs and warnings, and more.
Still, some people consider that Safety is the outcome of performing 5S appropriately. Thus, saying that the 6th S is not necessary.
Neither approach to the 6th S is right or wrong. Nevertheless, if you prioritize your employees’ safety, as any business should, or if the workplace can be quite hazardous, then Safety is as important as the other steps.