The Ultimate Guide to Buying The Right Packaging Equipment
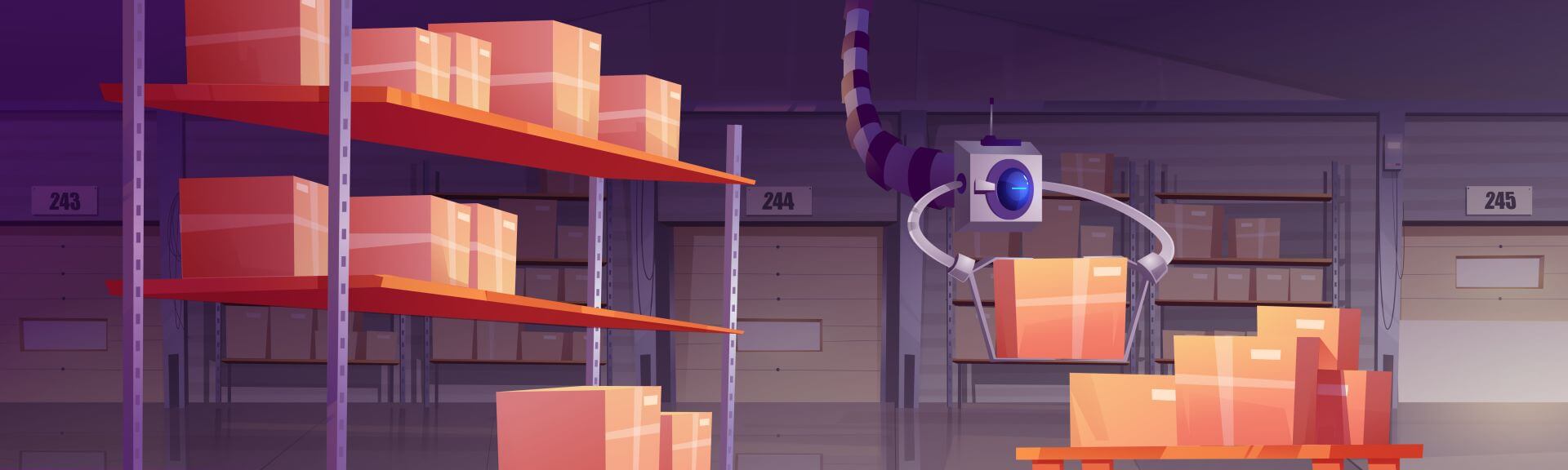
Investing in new packaging equipment might be a step toward business growth and increased revenue. There are several things to consider when purchasing packaging machinery, from studying machinery manufacturers, models, and brands to selecting a service, project procurement, and preventative maintenance vendor.
When considering purchasing a new packaging machine, you should research and engage in due diligence in the process. This guide will give you all the knowledge you need and then some on how to buy packing equipment from Millennium packaging company.
When Do You Need Packaging Machinery?
Every piece of packaging equipment has a limited lifespan. In the case of packaging systems, the average life expectancy is 10 to 15 years. Business owners, managers, and operators will be acutely aware of packaging challenges such as an expiring machine requiring increased maintenance or producing broken or faulty packs. If the expense for repair work is too high, or if repair work will not make the machinery operational again, it is time to replace it.
You may also need to install equipment to boost capacity to meet customer demand or to prepare for development into new markets. You could bring the packing operation in-house from outside packers. You might also be entering the packaging industry for the first time.
Whatever your reason for purchasing new packaging equipment, you must address the following challenges:
- Budget
- Specification
- Sourcing
- Scheduling
- Installation, testing, and systems integration
- Training
- Maintenance and support
What Are the Components of Packaging Equipment?
Individual pieces of packaging equipment serve specific duties, and a specification for each of these is part of the purchasing process. The significance of this is that the performance of the equipment as a whole is limited by the performance of its slowest or least trustworthy component.
The following are the main components of packaging machines:
Conveyors including chains, belts, and drivers
Horizontal conveyors are the primary means of transporting items and packs through the packaging process. The propulsion, such as an electric motor or, less typically, compressed air, and whether the conveyor employs belts or rollers are essential considerations.
Solid fillers (weight, volumetric, count)
Checkweighers, volume controls, or an automated count of the number of solid units entering into each pack are used to measure solids. Filling equipment for loose-flowing powders and grains similar to that used for liquids are all crucial considerations for the manufacturing process.
Liquid fillers (volume or level)
Gravity or pumping can be used to fill liquids controlled by technology that fills by a measured volume level or up to a predetermined level via a doser.
Container handling
Examples of packaging materials include flexible bags, glass bottles, and metal containers. Each container must be handled manually or by technology that uses push feeding, basic grabbers, or more advanced collaborative robots.
In the realm of sustainable and environmentally friendly packaging solutions, choosing plant-based screw top containers can be vital. These options ensure the safety and integrity of the product and align with brand values geared towards sustainability. They leverage materials that are FDA-approved, BPA-free, and distinctly crafted in the USA to meet diverse sizing requirements.
Capping
Capping machines feed circular disks from a hopper for crimping around bottle tops using a chuck.
Vacuums and modified atmospheres
Vacuum packing is an essential technique for increasing food products’ shelf life and preserving medications and other products from moisture and other possible harm.
A vacuum is created using pumps. To avoid food degradation, modified environment packaging employs pumps that replace oxygen with inert gases such as nitrogen.
Wrapping equipment
Film wrapping is an essential aspect of packaging. Examples include wrapping drink film around an object and shrinking it using heat to make a tight wrap. Or using packaging material such as a stretch wrapper around a product and flexible film forms a tight-fitting barrier to protect the goods and preserve product quality.
Stretch wrapping equipment is used in packaging a wide range of products, from bite-sized snacks and baked goods to piled pallets of cartons.
Form fill seal machines
Form fill seal machines (FFS) provide complete packaging solutions. Beginning with the manufacture of packs (bags, pouches, or cartons), filling with products, sealing and wrapping, and continuing through production line processes such as cartoning and palleting.
Labeling machines
Labels play a vital part in packaging, serving a variety of functions ranging from product codes and logistical information to consumer-facing information such as best before dates, marketing messages, and branding.
Labeling solutions range from basic reel label applications to customized, data-driven label printing and application.
Inspection equipment
Inspection equipment is essential for guaranteeing packing quality, uniformity, and safety. Many packing procedures involve visual inspection by human operators. However, there are more possibilities based on advanced 2D and 3D machine vision systems. Magnetic and x-ray inspection instruments, for example, are used to detect metallic pieces in food products.
Case sealers and cartoning
As packages are completed, they are frequently placed in cartons that have been constructed within the packaging plant by a case erector.
The cartons are positioned manually or automatically at the end of the packaging line. They are filled with products with equipment based on gravity, conveyors, grippers, robotic arms, and other machines. Filled cartons and cases are usually forwarded to pallets for shipping or storage.
Sourcing Your Professional Packaging Systems
After completing your specification, it is time to approach manufacturers and equipment dealers. Unless you work in a highly specialized packaging sector, such as dangerous goods, the options are numerous.
What you have heard from business connections and what your investigation reveals about possible suppliers are likely to determine who you approach for quotations.
New or Used Packaging Machinery?
With a huge number of packaging equipment manufacturers to pick from and many machine models, new equipment is frequently the first consideration for purchasers. New machinery may provide additional financing choices, such as lease and renting. However, wait times might be significant because manufacturers do not often offer ‘off-the-shelf’ equipment, save for smaller machines and components.
You should not dismiss the possibility of purchasing secondhand packaging equipment since it may be the most economical solution. Previously owned equipment is usually readily accessible, and some have never been used.
Secondhand machinery, whether pre-owned or not, must be:
- per your specific needs
- with a spotless pedigree
- ready for inspection and testing
- free of flaws
- accompanied by a guarantee or is returnable
Furthermore, if adjustments to used equipment are necessary, you must know how much they will cost and how they will be carried out.
Key Takeaways
- Research and due diligence are crucial when upgrading packaging equipment.
- Consider the lifecycle of packaging machinery and strategic needs for updates.
- Plan meticulously across budgeting, specification, sourcing, and implementation.
- Weigh the pros and cons of new versus used machinery based on business needs.
- Ensure informed decision-making for operational efficiency and customer demand fulfillment.